Mehr Komfort und Effizienz: die neue Fördertechnikanlage bei Frank Flechtwaren steigert den Output ohne zusätzliches Personal
Bei Frank Flechtwaren zeigt FÖRSTER & KRAUSE, wie die Kombination aus optimierter Materialflussstrategie, moderner Fördertechnik und ergonomischen Arbeitsplätzen Wachstum auch da möglich macht, wo Arbeitskräfte schwer zu finden sind.
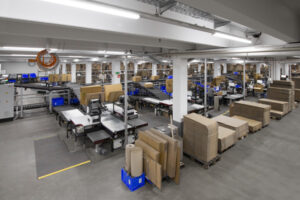
Fördertechnik für Kommissionierung und Warenausgang
Trotz aller Krisenmeldungen sind im Onlineshopping noch immer große Wachstumsraten möglich. Gerade im Bereich Interieur und Dekoartikel boomt das Geschäft aktuell – auch dank vieler erfolgreicher Influencer in den sozialen Medien. Allerdings kann eine schnelle und große Erweiterung des Geschäfts besonders in der Logistik ganz neue Herausforderungen mit sich bringen, wie die Frank Handels GmbH & Co. KG (besser bekannt als Frank Flechtwaren) feststellen musste. Denn Arbeitskräfte für Kommissionierung und Verpackung, auf die es beim Onlineversand besonders ankommt, sind heute schwer zu finden. Glücklicherweise kann durch die richtige Planung und Technik Abhilfe geschaffen werden.
Das Unternehmen vertreibt hauptsächlich Wohn- und Dekoartikel mit großem Erfolg. Dank dieses Erfolges wurde es aber im Bereich Logistik knapp. Deshalb plante Frank Flechtwaren eine bestehende Anlage durch neue Fördertechnik zu ersetzen. Hier kamen FÖRSTER & KRAUSE ins Spiel, die mit dieser Aufgabe betraut wurden.
Vorteile auf einen Blick
Anzahl der Packplätze: 35
„Natürlich ging es nicht nur darum, die bestehende Technik durch eine neuere Version zu ersetzen. Zu den weiteren Zielsetzungen gehörte es, auf der bestehenden Fläche einen größeren Automatisierungsgrad zu erreichen, bei dem das Handling der Behälter und gepackten Pakete reduziert wird.“
Flexible Arbeitsweise und optimierte Arbeitsplätze
„Natürlich ging es nicht nur darum, die bestehende Technik durch eine neuere Version zu ersetzen“, erklärt Markus Förster, Geschäftsführer bei FÖRSTER & KRAUSE. „Zu den weiteren Zielsetzungen gehörte es, auf der bestehenden Fläche einen größeren Automatisierungsgrad zu erreichen, bei dem das Handling der Behälter und gepackten Pakete reduziert wird.“ So sollte auch ein höherer Durchsatz möglich werden, der den aktuellen Anforderungen des Unternehmens entspricht.
Die Motivation hinter dem Projekt war aber nicht rein technisch begründet. Denn am Ende kommt es ganz besonders auf die Mitarbeiter an, die beispielsweise an den Packplätzen ihre Arbeit verrichten. Durch den bestehenden und sich in den nächsten Jahren noch verstärkenden Fachkräftemangel war klar, dass die neue Anlage sicherstellen muss, dass ein Wachstum bei den Bestellungen mit einer gleichbleibenden Zahl an Mitarbeitern machbar ist. Außerdem sollten die Mitarbeiter durch ergonomische Arbeitsplätze möglichst umfassend geschont werden.
Diese Überlegungen führten auch zu einem besonderen Detail, das für die Planung der Anlage von großer Bedeutung war: eine flexibel anpassbare Arbeitsweise möglich zu machen. So ist es in Zeiten mit einem hohen Bestelleingang möglich, dass gleichzeitig an den Arbeitsplätzen für die Kommissionierung und die Verpackung gearbeitet wird. Ist die Auslastung geringer, können die Mitarbeiter beispielsweise am Vormittag vorwiegend kommissionieren und am Nachmittag zum Verpacken übergehen.
Detaillierte Planung als Grundlage für den Erfolg
Möglich wird das über einen entsprechenden Puffer. Dieser Puffer fasst in diesem konkreten Fall 218 Aufträge, die kommissioniert werden können, bevor sie am Packplatz abgearbeitet werden. Insgesamt 35 dieser Packplätze bietet die neue Anlage. 22 davon werden für Kleinaufträge genutzt. An den übrigen 13 Packplätzen werden besonders große Kartonagen gepackt.
„Aber das ist natürlich nur ein Detail aus diesem Projekt, dem eine detaillierte Planungs- und Konzeptphase vorausging“, führt Markus Förster aus. „In dieser Phase haben wir in einem Trio aus Kunden, dessen externen Beratern und unseren Experten gearbeitet. Gemeinsam haben wir die Anlage so geplant, dass sie den langfristigen Wachstumsprognosen von Frank Flechtwaren entsprechen kann. Aber unseren Auftraggebern war es auch ein Anliegen, die Anlage so ergonomisch und mitarbeiterfreundlich wie möglich zu gestalten.“
Heute können die Behälter direkt vom Kommissionierwagen auf die Fördertechnik geschoben werden, ohne dass sie gehoben werden müssen. Auch die bereits beschriebenen 22 Packplätze für Kleinaufträge sind höhenverstellbar. So können die Mitarbeiter sie immer in die perfekte Position für den zu packenden Karton bringen. Einmal gepackt, werden die Kartonagen und Leerbehälter wieder direkt auf die Fördertechnik geschoben, wodurch die Mitarbeiter maximal geschont werden. „Die Basis für diese Auslegung der Anlage waren Gespräche mit unseren Mitarbeitern im Rahmen der Planungsphase“, so Stefan Aprill, Betriebsleiter bei Frank Flechtwaren. „Am Ende wissen unsere Mitarbeiter am besten, was sie brauchen und wie man den Wohlfühlfaktor erreicht, der uns wichtig war.“
„Die Basis für diese Auslegung der Anlage waren Gespräche mit unseren Mitarbeitern im Rahmen der Planungsphase. Am Ende wissen unsere Mitarbeiter am besten, was sie brauchen und wie man den Wohlfühlfaktor erreicht, der uns wichtig war.“
Stefan Aprill, Betriebsleiter bei Frank Flechtwaren
über Frank Flechtwaren
Die Geschichte von Frank Flechtwaren reicht bis ins Jahr 1885 zurück. Gegründet wurde das Unternehmen im Erzgebirge mit dem Ziel, Spankörbe und Emailleartikel herzustellen. In den 1950er-Jahren siedelte das Unternehmen nicht nur in die Südwestpfalz um, sondern legte mit den ersten Katalogen, in denen das Korbsortiment des Unternehmens präsentiert wurde, den Grundstein für einen erfolgreichen Versandhandel. Über die folgenden Jahrzehnte wurden nicht nur die Kataloge durch einen Onlineshop ergänzt, auch das Sortiment von Frank Flechtwaren wurde deutlich erweitert. Heute vertreibt das Unternehmen hauptsächlich Wohn- und Dekoartikel.
Mehr Leistung und mehr Komfort für die Mitarbeitenden auf gleicher Fläche
Das Besondere am finalen Ergebnis ist, dass die Anlage nicht nur mehr Komfort für die Mitarbeiter bietet, sondern gleichzeitig auf der bestehenden Fläche mehr Output bei gleichbleibender Mitarbeiterzahl möglich macht. Insgesamt können im Bereich der Kleinteileverpackung jetzt 1.540 Einheiten (Behälter oder Kartons) pro Stunde transportiert werden. Jeder der 22 Packplätze für Kleinaufträge verfügt über 6 Pufferplätze, in denen insgesamt 132 Kommissionierbehälter Platz finden.
Hinzu kommt ein Loop, auf dem sich zusätzliche 46 Kommissionierbehälter im sogenannten aktiven Puffer befinden können. Gemeinsam mit der Zuführung, die Platz für 40 Kommissionierbehälter bietet, ergibt sich die bereits angesprochene Summe von 218 Aufträgen, die auf der Fördertechnik gepuffert werden können. Insgesamt hat die Anlage eine Länge von 765 Metern und die Kommissionierbehälter und Kartonagen bewegen sich mit einer Geschwindigkeit zwischen 0,4 bis 0,8m/s.
Kommissioniert werden die Behälter zunächst auf Elektro-Transportroller mit angehängtem Kommissionierwagen, über die Frank Flechtwaren schon zu Beginn des Projekts verfügte. Auch von diesen Fahrzeugen können die Behälter ohne großen Kraftaufwand direkt auf die neue Fördertechnik geschoben werden. Die Fördertechnik führt sie dann den Packplätzen zu.
Die Rückführung der Leerbehälter geschieht danach ebenso automatisch, wie der Abtransport der Versandkartonagen zu den fünf Versandtoren, wo die Pakete über die abgehängte Fördertechnik auf Teleskopgurtförderer sortiert werden. Die Leerbehälter wiederum werden den Mitarbeitern auf vier Bahnen zur erneuten Kommissionierung bereitgestellt. Der Leerbehälterbahnhof ist strategisch gegenüber der Stelle platziert, an der bereits kommissionierte Aufträge abgegeben werden. Dadurch wird sichergestellt, dass kurze Wege und effizientes Arbeiten auch in diesem Schritt gewährleistet sind.
„Dem Wunsch nach mehr Leistung auf gleicher Fläche wurden wir unter anderem durch Deckenabhängungen und ein doppelstöckiges Design der Fördertechnik gerecht. Durch die Optimierung der Materialflussstrategie, zu der auch die Leerbehälterrückführung gehört, konnten wir außerdem sicherstellen, dass die Mitarbeiter bei Frank Flechtwaren ihrer eigentlichen Kerntätigkeit nachkommen können und deutlich weniger manuelles Handling nötig ist.“
Ergonomische Packplätze und automatisierte Materialflüsse – so arbeiten Mitarbeiter gerne!
„Dem Wunsch nach mehr Leistung auf gleicher Fläche wurden wir unter anderem durch Deckenabhängungen und ein doppelstöckiges Design der Fördertechnik gerecht“, erklärt Markus Förster. „Durch die Optimierung der Materialflussstrategie, zu der auch die Leerbehälterrückführung gehört, konnten wir außerdem sicherstellen, dass die Mitarbeiter bei Frank Flechtwaren ihrer eigentlichen Kerntätigkeit nachkommen können und deutlich weniger manuelles Handling nötig ist.“
Welche Arbeitserleichterung der Wegfall von Hebetätigkeiten darstellt wird deutlich, wenn man sich die Dimensionen der großen Behälter mit einer Abmessung von 800 Millimeter x 600 Millimeter plastisch vor Augen führt. Die Maße entsprechen genau einer halben Europalette. Entsprechend schwer können die Behälter werden (leer > 7 kg) und entsprechend unhandlich sind sie für die Mitarbeitenden zu greifen.
Dass dieser Ansatz richtig war, konnte mittlerweile im Einsatz nachgewiesen werden. Wie Stefan Aprill berichtet, arbeiten die Mitarbeiter deutlich lieber an den neuen ergonomischen Packplätzen als an den alten Packplätzen. Dazu trägt auch die deutlich niedrigere Geräuschentwicklung der neuen Anlage bei.
Das könnte Sie auch interessieren
Benötigen Sie weitere Informationen?
Wie können wir Ihnen weiterhelfen?